Why do non-contact sensors have blind spots?
Each of us knows the advantages and disadvantages of non-contact sensor. But one of the biggest questions is about the blind spots that plague many people with non-contact sensors. As time goes by, because these problems do not have the proof of facts and explanation of professional knowledge, the technology of our one-sided task sensor manufacturer is defective, and the manufacturer does not spend much energy and cost on it.
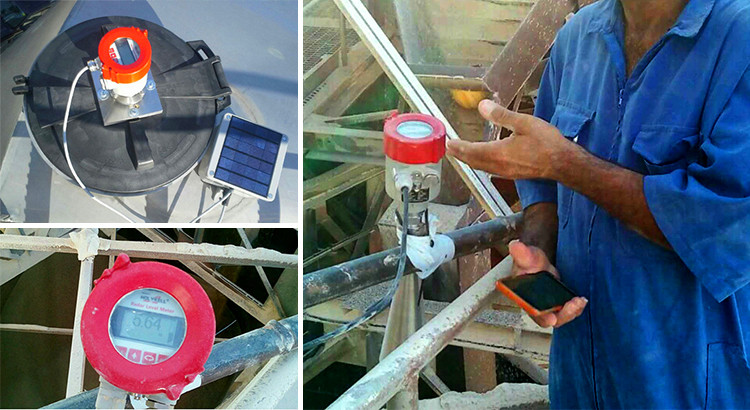
Strictly speaking, non-contact sensor is divided into high frequency radar level sensor and non-contact ultrasonic liquid level meter. These two non-contact sensors are basically used for the level monitoring of industrial medium (water, oil and corrosive medium), especially for the level measurement of corrosive and food-grade medium. Non-contact sensors are the best solution. Although it's advantages are obvious, it's disadvantages also stand out. The sensor cannot be used in the measuring environment with large range (measuring range is less than 30 meters). As the measuring range is larger, its blind area will be larger and the measurement results will be inaccurate. At present, there is no most effective way to solve this blind spot, and various manufacturers are using technical means to reduce the blind spot.
How to reduce blind spots?
In my opinion, the most effective way to solve the blind spot of non-contact sensors is to reduce the measuring range and avoid using them in noisy and dust-free environments. From a professional point of view, the blind spot belongs to the physical characteristics of the sensor, which cannot be eliminated. With the progress and development of science and technology, it can be reduced gradually. In addition, once we need a special range environment, we can choose input sensors or other types of industrial sensors.